“Simple enough for the everyday user but complex enough for our multifaceted business”
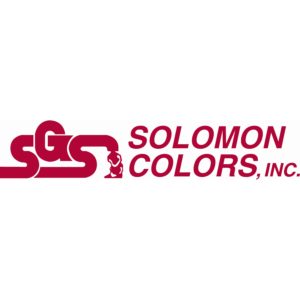
We spoke with Missy Nelson, Director of Inventory Control, with Solomon Colors about her experience with VicinityChem software.
The Situation
Solomon Colors is a family- and employee-owned and operated global leader in architectural concrete products. In business for over 90 years, it manufactures and distributes anything, and everything related to concrete – from colors to fibers, to polishes, to stamps. Solomon Colors has grown with its many acquisitions to meet the innovative demands of the market and has production facilities in IL, CA and MD and inventory warehouse spaces across the U.S. Solomon Colors has been a customer of VicinityChem since 2014.
The Solution
Because Solomon Colors is a process manufacturer, its volume-based formulas can change a lot for all its colored products across its different vendors. VicinityChem gives Solomon the flexibility to manage all the varied formulas and links all its facilities. This also helps better manage Solomon’s complicated inventory across its many facilities, as Solomon programs the software to let it know what needs to be made and what needs to ship from each location. As Solomon has grown, the system has grown with it to help manage the numbers at each location.
“The structure of the VicinityChem software is very well thought out. The components and formulas are linked so that they function well together, which works for Solomon Colors. With VicinityChem, you can just input two criteria that before could take up to an hour and a half to enter manually, and the work is done.”
Missy Nelson, solomon Colors
The Success
There are several factors that keep Solomon Colors loyal to VicinityChem, but the two most important are:
- VicinityChem fulfills all of its functionality needs
- The customer service immediate response and knowledge base is second to none
“No matter who you call in customer service at VicinityChem, the person on the receiving end will be able to help. Everyone there understands the software’s technology, production, and accounting. You don’t ever find that extensive knowledge base with other customer service people. And, if Vicinity doesn’t have the structure that we need, they will change it for us or add it to a future update.”
“In a nutshell, Vicinity is simple enough to use but complex enough to get the job done well.”
If you are interested in learning more about VicinityChem and how it can help your chemical manufacturing processes, connect with our team today.
Other articles you might like:
Case Study: Crowley Chemical Company
Case Study: Engineered Custom Coatings
5 must-have research and development tools